Welding with filler wire procedure
- aqcinspection
- Sep 12, 2020
- 2 min read
Welding is a process of joining two base metals by heating it. It can be done with or without additional filler metal being used. Below are the few types of welding process : 1)Shield Metal Arc Welding, 2) Metal Inert Gas Welding 3) Tungsten Inert Gas Welding 4) Oxygen fuel gas welding 5) Friction Stir Welding (no filler metal required) 6) Electric Resistance Welding (no filler metal required) and few more….
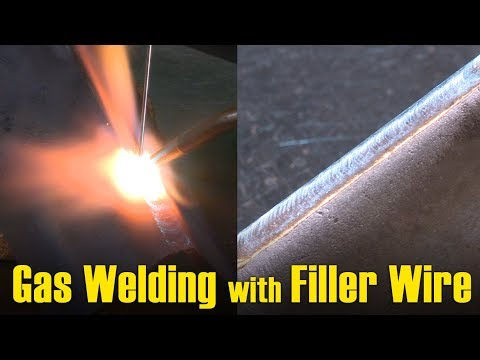
For welding with additional filler wires, care should be taken that the selected filler wire or electrode is compatible for the metal being joined.
Collect the Material Test Certificate of the material . Batch test certificate of the filler wire and verify the values.
First step is to check the chemical composition of filler wire. The minimum required chemical content should be present and maximum allowed chemicals should be restricted in the filler wire. If Carbon Equivalent value is restricted for the base metal then check the carbon equivalent value of the filler metal. Verify the value is maintained in the required level.
Second is to verify the Tensile strength of the selected filler wire material. The Tensile strength of the filler wire should be equal to or more than the Tensile strength of the material being joined. Being the materials joined are similar metals.
Third step is to verify the filler wire or electrode satisfies additional requirements such as low hydrogen content, impact toughness property,low temperature or elevated temperature toughness property, high temperature elongation property, Hardness values. If the base material to be joined are having those property then the filler wire electrode selected should posses those properties.
Finally the selection of size of filler wire or filler wire formed can be made as per the welding process. Thickness of the welded metal, root gap possibly present and amount of metal to be filled in a single pass.
An procedure qualification test shall be done with the selected filler metal on the sample test specimen. With a thickness in between the range of thickness to be welded. Care should be taken that the welding paremeters such as Current, Voltage, Welding Travel Speed, Heat Input value (kJ), Weld bead width, Weld metal thickness are all maintained at allowable limits. These limits are derived from previous experiences and practices said in standards.

After the test Weld has been made, it is non destructive tested for defects and accepted Weld specimen is cut and tested for its mechanical properties. All tests required to prove it’s required properties are done, before approving any welding process.
To qualify only the Welding electrode or filler wire, Tensile Test and all Weld mechanical tests are done. The sample for testing is cut only from the Weld metal, i.e longitudinally in the Weld. To qualify the whole welding procedure the mechanical test samples are cut in transverse to the Weld seam.
For more guidance to your welding process and more to qualify a welding procedure or selection of weld samples, welding failure analysis, welder qualification and Welder Certificate reach us at https://aqcinspection.com/
Also for non destructive testings NDT and mechanical testings for you PQR /WPS qualification, we have a dedicated facilities, to know more see https://aqcinspection.com/mechanical-testing-services/
Find our Blog updates from https://advancedqualitycentre.blogspot.com
Comments