Welding Safety
- aqcinspection
- May 31, 2022
- 4 min read
Welding Safety with Gas Cylinders
On an oxyacetylene system there will be three types of valves, the cylinder valve, the regulator valve, and the torch valve. There will always be a set of three valves for each system, since the gas in the cylinders is at high pressure.
A broken off valve will release extremely high pressures, which could cause the cylinder to become an extremely deadly flying missile. For this reason, never move an oxygen tank around without its valve cap screwed in place.
An oxygen tank is especially dangerous for the reason that the oxygen is at a pressure of 21 MPa (3000 lb./in² = 200 atm). Oxygen cylinders are generally filled to approximately 2200 psi.
The regulator converts the high pressure gas to a low pressure stream suitable for welding. It is not recommended to directly use high-pressure gas.
Pressurized cylinders must at all times be handled with great care. Shielding gases such as carbon dioxide, argon and helium are nonflammable and no-nexplosive.
The subtle welding safety points when using gas cylinders that should be followed are:
More than 1/7 the capacity of the cylinder should not be used per hour. This causes the acetone inside the acetylene cylinder to come out of the cylinder and contaminate the hose and possibly the torch.
Acetylene is dangerous above 15 psi pressure. It is unstable and explosive; Proper ventilation when welding will help to avoid large chemical exposure; Oxygas welding station – keep cylinders and hoses away from the flame; Keep cylinders away from any welding or other electrical circuits;
Never allow a welding electrode to touch any cylinder;
Install and secure cylinders in an upright position by chaining them to a wall, a portable cart or a stationary support to prevent from falling.
Chemical Exposure:
Exposure to certain metals, metal oxides, or carbon monoxide can often lead to severe medical conditions. Damaging chemicals can be produced from the fuel, from the work-piece, or from a protective coating on the work-piece.
By increasing ventilation around the welding environment, the welders will have much less exposure to harmful chemicals from any source. The most common fuel used in welding is acetylene, which has a two-stage reaction. The primary chemical reaction involves the acetylene disassociating in the presence of oxygen to produce heat, carbon monoxide, and hydrogen gas: C2H2 + O2 → 2CO + H2.
A secondary reaction follows where the carbon monoxide and hydrogen combine with more oxygen to produce carbon dioxide and water vapor. When the secondary reaction does not burn all of the reactants from the primary reaction, the welding process produce large amounts of carbon monoxide.
Exposure to zinc oxide fumes can lead to a sickness named “metal fume fever”. This condition rarely lasts longer than 24 hours, but is still unpleasant. Generally influenza, fevers, chills, nausea, cough, and fatigue are common effects of high zinc oxide exposure.
Complete Safety Equipment for Welders:
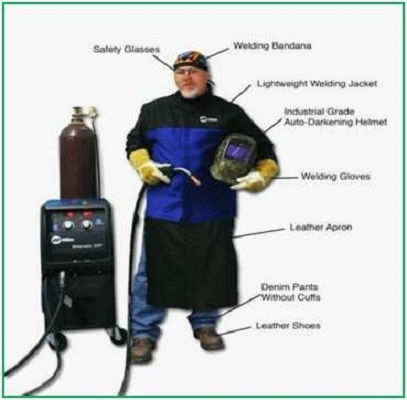
Flashback:
Flashback is the condition of the flame propagating down the hoses of an oxy-fuel welding and cutting system. To prevent this, a flashback arrestor is employed. The flame burns backwards into the hose, causing a popping or squealing noise.
It can cause an explosion in the hose with the potential to injure or kill the operator. Using a lower pressure than recommended can cause a flashback.
The Importance of Eye Protection:
Proper protection such as welding goggles should be worn at all times, including to protect the eyes against glare and flying sparks. Special welding safety eye wear must be used, both to protect the welder and to provide a clear view through the yellow-orange flare given off by the incandescing flux.

The goggles eye protection must be according to ANSI Z87-1989 – Safety Standards for Special Purpose Lens, designed especially for gas-welding aluminum that cuts the sodium orange flare completely and provides the necessary protection from ultraviolet, infrared, blue light and impact.
Hot Work Procedures:
The Inspector must ensure that all relevant check lists, certificates and work permits (WPs) for hot work have been issued. If work is being done outside the workshop, an assistant protected in the same manner as the welder, should accompany him.
If work has been done inside a confined space the assistant should be placed outside, within view of the welder and with possibility to cut off gas and power supply. (Gas quick couplings and unlocked safety cable connectors may act as emergency cut-offs).
Operator and Assistant Protection:
The Inspector should check the welder safety clothes, as well. Welder cannot wear clothes of highly combustible materials or wet clothes, and do not carry combustible material, e.g. matches, lighters, oily rags.
Welding gloves should always be used, and when necessary also use additional leather clothing for protection against sparks, heat and electric shock. The welder must use head and face protection (helmet, shield, goggles) and ensure that filter glasses are unbroken and have the correct shade.
we provide standard specifications for welding procedures for all welding process and Brazing. We offer Welder Procedure Specification, Welder Certificate Renewal Process, Procedure Qualification Record, Welder Qualification Testing, welder Training and Welder qualification services in Coimbatore,Trichy, Salem, Erode, Chennai.
Please feel free to reach us https://aqcinspection.com/training/ to learn more about any of the methods in detail.
Visit our technical and career updates at our Blog site https://advancedqualitycentre.blogspot.com . or
Comments